ERNEST: Sample Exchange
Robot
May - August 2019
ROLE
Controls and Robotics Student Research Intern
DESCRIPTION
Developing a highly precise robotic sample exchange environment using a 3-Axis piezo-electric powered manipulator. The system is a prototype, but designed for direct use in the Hard X-Ray Nanoprobe at Brookhaven National Laboratory.


THE PROBLEM
The sample exchange process at the Hard X-Ray Nanoprobe (HXN) beamline at the National Synchrotron Light Source-II (NSLS-II) in Brookhaven National Laboratory requires breaking the vacuum with subsequent thermalization of the microscope’s components which may take up to a few hours.
THE SOLUTION
To increase efficiency and throughput of the HXN end station it is beneficial to implement an internal automatic sample exchange system that enables a quick and reliable sample exchange process. I was hired as a summer intern to therefore develop such a system, informally named the Exchange Robot for the Nanoprobe Experimental Station, ERNEST.
SYSTEM FUNCTION
Performed system calibration for strain gauges and linear encoders for all axes
To ensure precision for the highly-sensitive system, I performed high-accuracy calibration and tested for position repeatability.
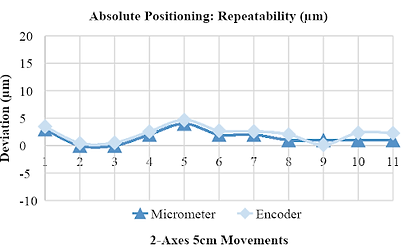.png)


Created animation to preview movements using Fusion360 simulation

The flowchart algorithm shows the standard sample loading, unloading, and management.
I designed the sample pegs, environment for manufacturing in the lab machine shop, and wrote the control algorithm in LabVIEW with accompanying GUI.
The piezo-electric linear actuators needed to achieve less than 10 nanometer precision in all movements, so force-sensing and placement was used for all actions to confirm positions.
.png)
CONTROL ALGORITHM DEMONSTRATION

PRESENTATIONS
I was selected to give a poster presentation and oral presentation to laboratory staff at the end of the internship.